Article Originally Published in SatMagazine
Author: Keith Brodek, Analysis Engineering Manager, Marotta Controls, Inc.
Pneumatic pressure regulation solutions are typically found in propulsion systems, present in launch vehicles (rockets), satellites, or ground-based support equipment essential to mission capabilities. Their impact is significant, as system failure could shorten or ground a mission. And yet, the ideal pressure regulation design choice is commonly left undefined or generalized in system-level models. This design practice is inadequate and hides the potential for unintended performance characteristics to be introduced into the system, often resulting in undesired consequences.
This approach also creates an environment where even experienced system- level engineers may not recognize the component-level impact of their design choices. When determining pressure reduction methods, they often stick with design choices successfully used in past systems, regardless of whether such a solution is ideal for performance, cost, and schedule.
To address this, the cognizant engineer must utilize a collaborative design analysis that is ideally performed by the component supplier. For example, Marotta’s analysis engineering team has developed an algorithm that enables quick-turn analysis, simulating pressure regulation response based on the application’s parameters such as fluid, performance, delivery time, and more.
To further streamline design analysis of system-level considerations, the company studied the capabilities of various pneumatic solutions in relation to common system-level application requirements. The study compares five pressure regulation designs in four primary system-level configurations, arming system engineers with deeper insight into which type of pressure-reducing solution produces the optimal result for their design parameters.
No single solution fits all system-level designs, and the study illustrates the potential pitfalls of oversimplifying pressure regulation selection. It is essential to recognize the interplay between system components, collaborating early in the design cycle to make strategic design trades that protect reliability, cost, weight, and a spectrum of other considerations foundational to mission-critical systems.
Analysis Drives Design Trades
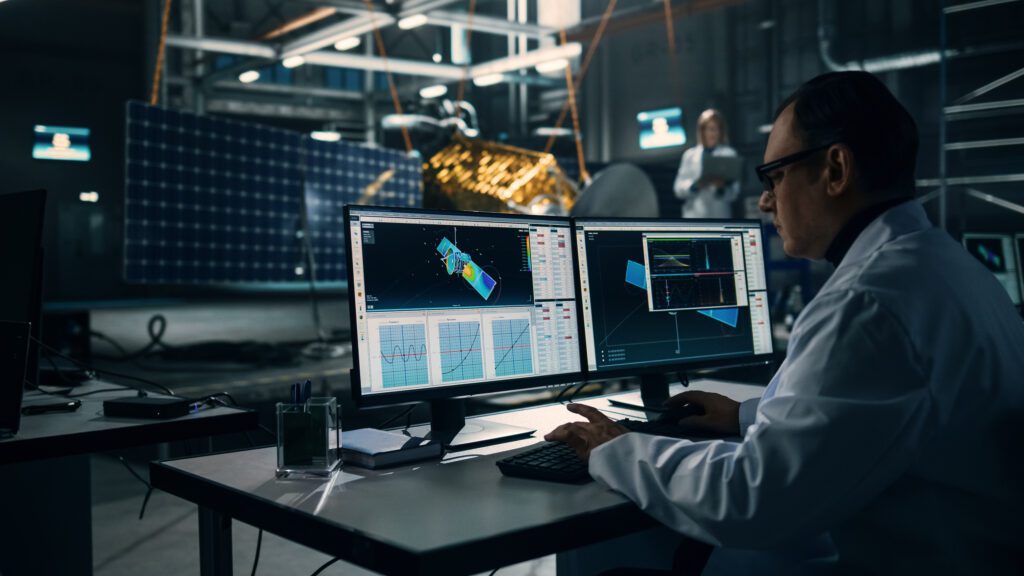
Each system-level design is unique and based on a set of parameters that are preferably optimized by the system engineer. In this process, the system engineer’s role is to determine the type of pressure regulation system most beneficial in meeting a spectrum of considerations.
For example, satellite integrators must often prioritize system weight as well as overall performance, given that NASA estimates costs of ~$10,000 to put a single pound of payload into space. The optimized pressure regulation system reduces payload mass to orbit, but this may not be the prime feature in a pressure solution chosen largely for its historical performance.
Mechanical and electromechanical regulation designs each deliver specific performance characteristics that must be considered in terms of end-to-end impact on the overall system design. These performance-critical systems must be based on design strategies that consider not just performance but also cost, longevity, and system integration that ensures optimal reliability.
Collaboration can make all the difference in revealing ideal options as well as pitfalls. The system integrator may have resolved the problem at hand many times over, yet the pressure solution provider has solved it more often and under more diverse parameters. Examining design trades reveals this phenomenon but is not always part of the early system-level design analysis.
Smart Design Trade-Offs Examine the Options
In the design trades study, the mathematical models associated with each pressure regulation system provide simulated performance characteristics. The comparison included a range of pressure reduction solutions, spanning mechanical and electromechanical options.Each option features an upstream high-pressure tank or compressor system, with the pressure regulation system reducing this inlet pressure to a setpoint and ultimately delivering a low-pressure output such as fuel tank pressure of a rocket engine or coolant through a nozzle.
Pressure input to the regulator comes from a reservoir, which is either blown down as a function of time or topped off via a compressor-type system. Flow output from the system is typically controlled via downstream control valves; however, some electromechanical options may also function as active controls.
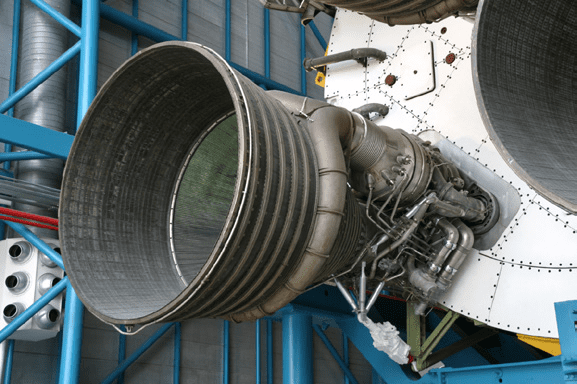
When considering the performance capabilities of any pressure reduction solution, there are certain system-level parameters that may be non-negotiable in terms of design trades. If a system strategy is already established and downstream components are selected, the pressure reduction solution must meet the requirements dictated by these existing design choices. For example, if a downstream component requires regulation to 1000 PSI, the pressure regulation solution must meet this need. For this design trade-offs study, this applies to pressure band, flow rate, and response time, which are locked down at an early stage of system-level development. Cost, schedule, weight, and reliability typically follow as top considerations.To accommodate the ideal balance among such factors, evaluate trades in performance, availability, and more as early as possible in the development cycle. The deployment environment may play the greatest role in prioritizing these considerations.
The study applied and analyzed this selection of pressure reduction solutions against four common system-level configurations with a series of defined parameters. While pneumatic pressure regulation is vital for system-level control in a broad range of aerospace systems, a large percentage of use cases includes cold gas thruster systems, electronics cooling systems, pressurant blowdown onto propellant for hybrid or mono-propellant engines, and bi- propellant liquid rocket engines.
The cold gas thruster case provides an example. Using a defined set of input conditions for this application, the analysis evaluated how various pressure reduction systems would perform. In this sample case, the spring-loaded pressure-reducing system, illustrated by Marotta’s RV74A-8A, outperformed other options graded on a scale of 1-10 on parameters including system weight, regulation band, reliability, simplicity of the solution, time to delivery, and cost.
In this instance, spring-loaded pressure reduction offered consistent flow output without being oversized or overly complex – yet this solution was not optimal in every use case evaluated
Contrast these results to a case featuring pressurant blowdown onto propellant for a hybrid/mono-propellant engine. Because this pressure case includes a variable set point, performance requirements immediately eliminated the non-electronic valves such as exclusively passive spring-loaded options. If the satellite manufacturer or integrator most values cost and weight in their design, the electromechanical system would be optimal. If they value consistent regulation, then the electronic dome-loaded valve would provide ideal performance.
Without considering the differences between mechanical and electromechanical pressure regulation options, aerospace design engineers may create unwanted impact on system-level operations. Yet system-level engineers may unintentionally oversimplify their pressure reduction needs, embracing an idealized solution without recognizing a spectrum of dynamic factors that affect performance. By collaborating early in the design cycle, system-level engineers can access the most optimal pressure reduction solution, protecting ideal timelines, overall costs, and reliable performance.
Author Keith Brodek is an Analysis Engineering Manager at Marotta Controls, Inc., a fully-integrated solutions provider that designs, develops, qualifies and manufactures innovative systems and sub-systems for the aerospace sector. Keith’s focus is mechanical engineering in aerospace applications. Connect with Keith at [email protected] or LinkedIn.