Article by Maurizio Di Paolo Emilio | Originally Published in Power Electronics News
Marotta Controls announced the availability and final qualification of the PS11200, the fourth variant of the 1-STEP product line. This switching power supply delivers 11,200 W of fully isolated output power with 91% efficiency at full load. It is designed to replace legacy 400-A solutions that typically produce unregulated or loosely regulated power in a larger footprint. The PS11200 is rated at 11,200 W (28 VDC 400 A) with a three-phase input power of 115 VAC, 50 Hz to 800 Hz.
In an interview with Power Electronics News, Michael Germinario, senior technical director at Marotta, highlighted that the PS11200 has passed all qualification tests necessary to ensure the reliability and performance of the power converter within harsh environments commonly presented by military/heavy transport aircraft such as C-130 Hercules cargo planes and CH-47 Chinook transport helicopters, as well as unmanned aerial vehicles.
AC to DC for Harsh Environments
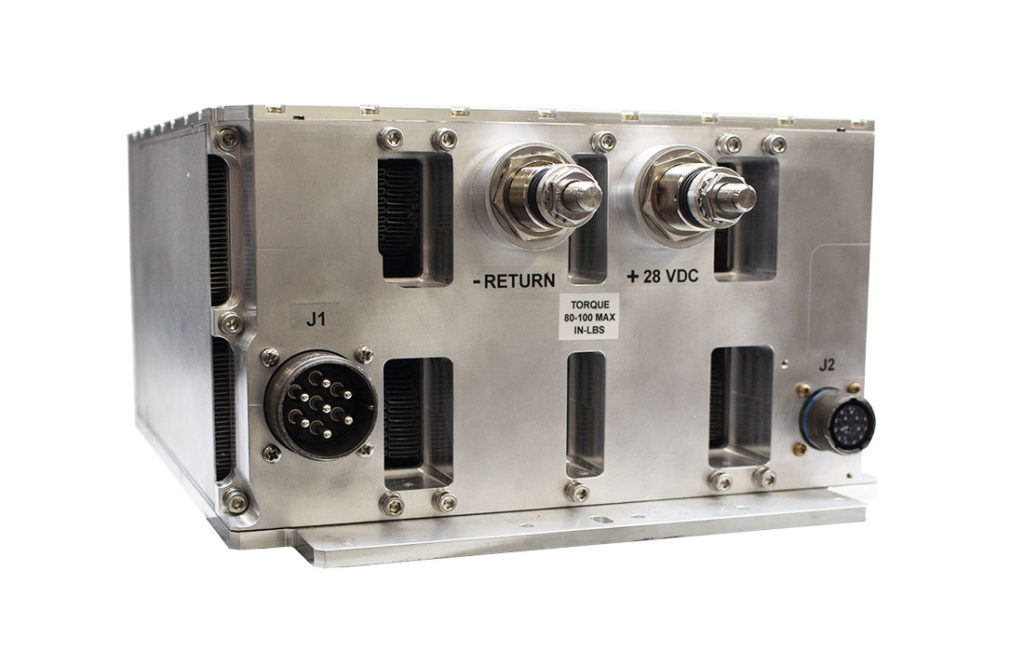
The steps involved in converting a three-phase AC power supply add their own complexity and components, contributing to the loss of efficiency and adding mass. In turn, designers are involved in tradeoffs in terms of size, weight, power, and cost. The aim of the AC-DC 1-STEP, as Germinario said, is to minimize these tradeoffs.
1-STEP converts AC input power to DC output power in a single, simplified conversion step to reduce weight, cost, and risk in a wide range of commercial and military applications. A 1-STEP converter is a circuit solution that achieves active power-factor correction, output voltage regulation, and electrical isolation in a single conversion step.
“1-STEP also delivers numerous other advantages such as higher reliability, less harmonic distortion, and the ability to step up or step down output voltage, to name a few,” said Germinario.
“Performance in terms of temperature, humidity, and shock vibration are important elements to consider,” he added. “Humidity is related to protecting the electronics with a conformal coating. And that’s where we need to focus to make sure we meet the environmental requirements. This focus is applied to all aspects of having a flight-worthy design.”
The key is to achieve maximum efficiency by minimizing the thermal load in the first place. “We use silicon carbide components and high magnetic permeability materials to increase efficiency,” said Germinario. “But we are also looking at GaN FETs in possible implementations.”
“Silicon carbide offers better characteristics in terms of voltage and current capability, and it all depends on how fast you want to switch and how low our RDS(on) is when selecting devices,” he added. “Faster switching can lead to smaller magnetic designs. We have taken advantage of both SiC and GaN devices to do that.”
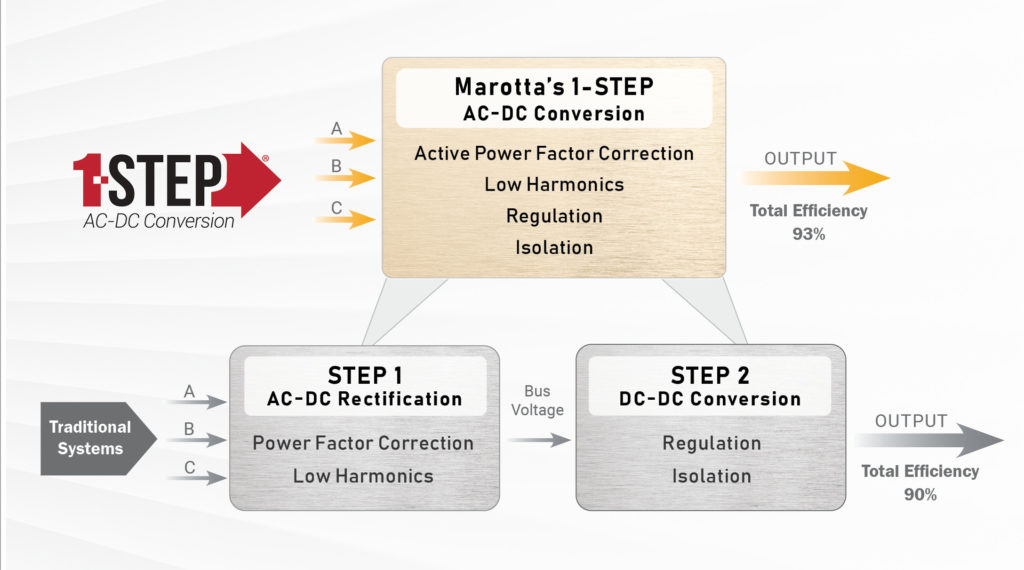
SiC’s advantages over silicon, in terms of achieving higher switching frequencies and low conduction resistance, have been widely recognized. Most of the benefits are associated with the superior material properties of SiC compared with silicon that result in faster switching speed and lower loss improvements. However, there is a general misconception in the engineering community that the challenges related to the design and selection of an optimal operating environment (gate drive and choice of passive components) reduce the benefits, thus limiting the usability of SiC devices. However, these have been resolved, and the solutions to those issues make wide-bandgap components less risky to develop.
Technological maturity, performance, and a significant reduction in cost due to increased volume and competition are the main reasons why SiC devices are being deployed in more and more applications.
Low switching losses allow an increase in switching frequency and a reduction in the size of passive components (capacitors, inductors), resulting in a reduction in the system’s cost, size, and weight. The size reduction is more or less proportional to the increase in frequency.