High Performance, Low Power
As spacecraft become smaller, so do the corresponding power generation devices, such as solar arrays. Satellite thermal management becomes a bigger issue with increased difficulty to dissipate heat from power consuming satellite components. As a result, smaller micro-spacecraft demand that less power be consumed by spacecraft components.
Marotta’s unique cold gas microthruster (CGMT) and electronics driver combination is capable of very low power operation. The resulting low power cold gas propulsion micro component provides an order of magnitude reduction in solenoid coil heating compared to an ordinary continuous duty solenoid.
- Satellite Propulsion
- Spacecraft Propulsion
- Attitude Control Systems
- Reaction Control Systems
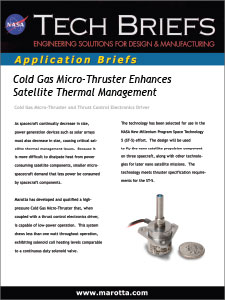
Fill out the form below to download CGMT Tech Briefs Article
Cold Gas Microthruster
The flight-qualified cold gas propulsion system yields high efficiency to achieve full performance in challenging thermal environments using passive cooling techniques.
- Less than 5 milliseconds response time
- Operating temperatures -18°C to 50°C
- GN2 or inert gas
- Less than 1 watt peak power
- Thruster Mass < 60 grams
Fill out the form below to download CGMT
Why Choose Marotta Controls?
When there is no margin for error, manufacturers in the world’s most demanding industries turn to Marotta Controls for control systems expertise. We have designed, developed and manufactured the most innovative products available anywhere since 1943. Examples of our work can be found in precision applications for the aerospace, marine and defense sectors. Our mission is to ensure the success of our customers, and we are committed to providing world-class support and a diverse product portfolio to accomplish that. We continue to innovate so that we can meet our customers’ needs now and well into the future.
Frequently Asked Questions
A cold gas microthruster uses pressurized gas such as GN2 to produce thrust without combustion. This makes it ideal for precision maneuvering, as it doesn’t rely on chemical reactions that can introduce variation or the risk of explosions. Most commonly, they are used for satellite propulsion and attitude control as well as spacecraft orientation.
Because they consume less than 1 watt at peak power, typically weigh less than 60 grams apiece and give off minimal amounts of heat, cold gas thrusters are a perfect fit for smaller spacecraft. This is because small satellites usually achieve minimal power generation from their solar arrays and frequently experience heat dissipation issues due to their compact size.
Our microthrusters are designed to deliver high-performance capabilities, with a response time of less than 5 milliseconds and reliable operation in temperatures ranging from -18 degrees Celsius to 50 degrees Celsius. Their innovative low-power design also enhances energy efficiency and they are adaptable for numerous mission profiles.
Compared to reaction wheels, these offer lesser power draw and a simpler design. Unlike chemical thrusters, they don’t rely on combustion that typically requires more complex systems and ground exposure risk. When integrated into attitude control systems, these microthrusters provide smooth, controlled adjustments in orbit without drawing large amounts of power.
In general, our microthrusters are used with gaseous nitrogen (GN2), because of its stability and availability. However, other inert gases can be used for specialized applications.
We subject all our microthrusters to rigorous flight qualification and testing, including environmental stress screening and vibration and shock testing. We are dedicated to optimized designs that provide long-term operational stability, with minimal moving parts and redundant engineering safeguards.
Our designs can be found in a wide range of aerospace applications, including satellite propulsion systems as well as spacecraft attitude control systems and reaction control systems. They all require exceptional performance and dependability, and that’s exactly what our components are designed to deliver.