State-of-the-Art Facility
Our vertically integrated operations ensure assembly and test procedures are streamlined to deliver the highest-quality, qualified control systems on-time. Our ability to design & develop customized aerospace testing equipment to meet stringent requirements in extreme environments enables us to deliver the highest performing solutions to our customers.
The majority of components/systems produced by Marotta Controls are “active control products” requiring 100% final acceptance testing. To achieve this requirement, Marotta Controls maintains complete on-site, high-performance materials testing capabilities.

Pneumatic Testing
- 40 pneumatic test benches
- 33 pneumatic test benches @ 6,000 psi
- 11 pneumatic test benches @ 15,000 psi
- Flow rates of 150 SCFM
- Grouped testing for up to 25,000 psi throughput
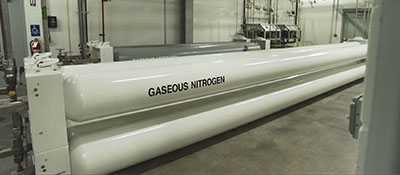
High Flow Testing
- Gaseous nitrogen high flow capability
- 2 piping systems up to 7,500 psi
- Up to 35,000 SCFM flow rate
- High compressor capacity and large nitrogen storage
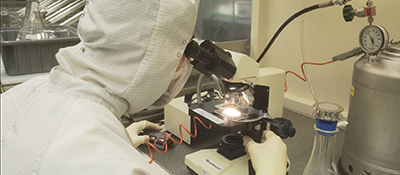
Special Fluids
- Ammonia
- Freon
- Helium
- Hydraulic Oil
- Hydrogen
- Hydrogen Peroxide
- Inert Gas
- Isopropyl Alcoho
- Krypton
- LNG
- Nitrogen
- Oxygen
- RP-1
- Skydrol
- TEA-TEB
- Xenon
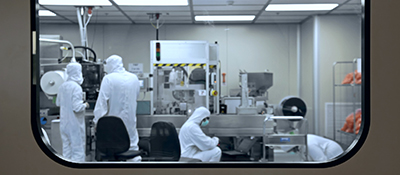
Clean Room
- 1,000 ft² Class 10,000/ISO 7 clean room on-site
- FED-STD-209
- 8 Flow Benches (Class 100) with flow hoods
- Nonvolatile Residue Analysis:
- Grade A Isopropyl alcohol filtered through 0.3 micron membrane, readable down to 0.01 mg
- DC-190 high temperature total organic carbon analyzer used with deionized water filtered through 0.2 micron membrane, readable to parts per million
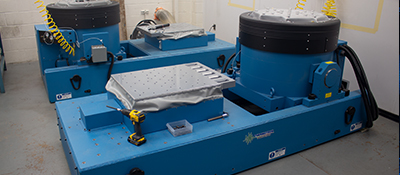
Vibration Testing
- Air cooled electrodynamic shaker system
- Up to 4,000 lbs of force (lbf)
- Velocities up to 70 inches per second (ips)
- Payloads up to 1,000 lbs
- Electromechanical actuation and power systems testing
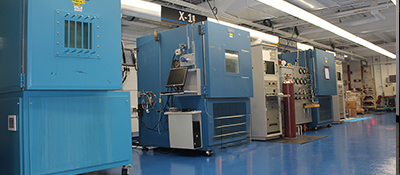
Thermal Altitude Testing
- Altitude simulation up to 120,000 ft
- Therrnal testing from -100ºF to 400ºF
- 15 thermal chambers on-site to perform tests simultaneously
- Vacuum testing to simulate up to 10-7 TORR
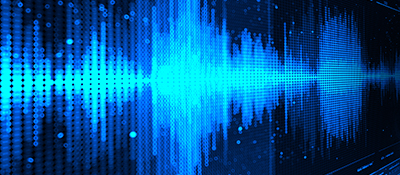
Acoustic Testing
- 1,600 ft² acoustic testing facility
- Structureborne & airborne noise testing
- Dual acoustic chambers for low and high pressure testing
- Test to less than 40 decibels for frequencies of 8 to 16,000 Hz
- Blowdown through 2″ & 4″ lines directly from tank to atmosphere
- Flow rate up to 270,000 SCFM at 6,300 psig
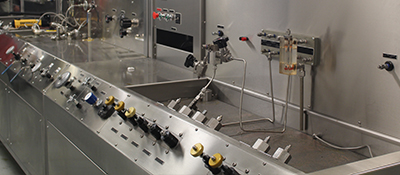
Hydraulic Testing
- 4 high pressure, high flow hydraulic test units on-site
- Flow rates of 25 GPM at 5,000 psig (MIL-H-83282 & 5606)
- Short duration pressures up to 10,000 psig of CTFE (MIL-H6083 or 5606 hydraulic fluid)
- Flow rates of 30 GPM at 6,000 psi Skydrol LD-4
- Flow ratess of 30 GPM at 1,500 psi of Lub Oil (MIL-PRF-23699)
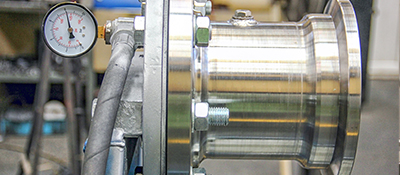
Hydrostatic Testing
- Fluids testing up up to 60,000 psi
- Gaseous Nitrogen or helium testing up to 25,000 psi
- Walk-in proof chamber permits full operational control and visual assessment through bullet-proof glass viewing window
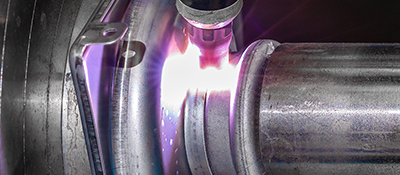
Welding
- Laser, electron beam & gas tungsten arc welding (GTAW) beam
- Certified nondestructive level 3 inspectors
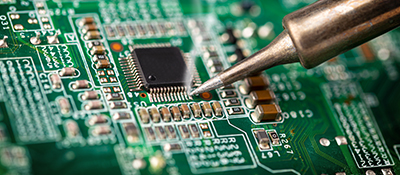
Soldering
- Soldering in accordance with IPC-J-STD-001
- Space hardware soldered to IPC-A-610 & NASA STD-8739.3
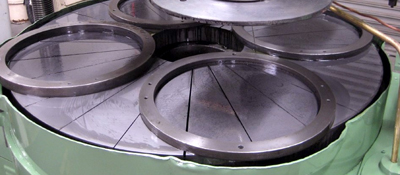
Lapping
- In-house capability to achieve ± 1 µ
- Flatness to ± 0.000001″