Control Actuation Systems
High Performance Electromechanical Actuation
Our advanced, high power density Control Actuation Systems (CAS) are designed to meet the challenging performance requirements for today’s advanced aerospace and weapons platforms.
Our on-site capability to design, test and qualify all unique components, assemblies and software/firmware enables our experienced engineering team to develop customized, high-efficiency electromechanical actuator solutions.
All mechanical, electronic and software elements are fully integrated and suitable for fin or canard control applications and are designed to achieve high slew rates under high loads in extreme environments.
We provide control solutions to actuate missile fins, doors and thrust controls for a multitude of applications. Our electromechanical actuation systems can be found in tactical missiles, guided munitions, unmanned aerial vehicles (UAVs), guided rockets and a myriad of other platforms where extreme precision and high performance are critical. Download the data sheet for more information about the specifications for our complete electromechanical missile control actuation systems and related product offerings.
- Tactical Missiles
- Hypersonic Vehicles
- Torpedoes
- UUV
- UAV
- Guided Munitions
- Guided Rockets
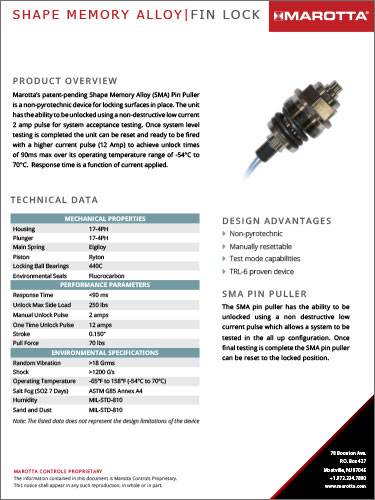
Fill out the form below to download SMA-Fin-Lock
Control Actuation System Capabilities
The wide range of capabilities offered by our missile fin actuators and related solutions mean high performance under even the most demanding conditions. These capabilities include:
- High power density, minimal envelope
- Fin/canard stow, deploy and locking capabilities
- High G
- High temperature thermal environment
- High power density: 32+ kVA total system output
- Up to 60 Hz Response
- Processing, DSP and FPGA
- Low voltage power supplies
- Full on-site design & development
- EMI/EMC circuitry
- Rapid, accurate response at hypersonic speeds
- Electromechanical actuation design
- Rotary (up to 6,000+ in-lbf)
- Mixed gear solutions
- Linkage systems (drag link/slider crank)
- Linear (up to 10,000 lbf)
- Ballscrew
- Planetary roller screw
- Jackscrew
- Rotary (up to 6,000+ in-lbf)
Missile & Torpedo Fin Control Actuation Systems
Hypervelocity Control Actuation Systems
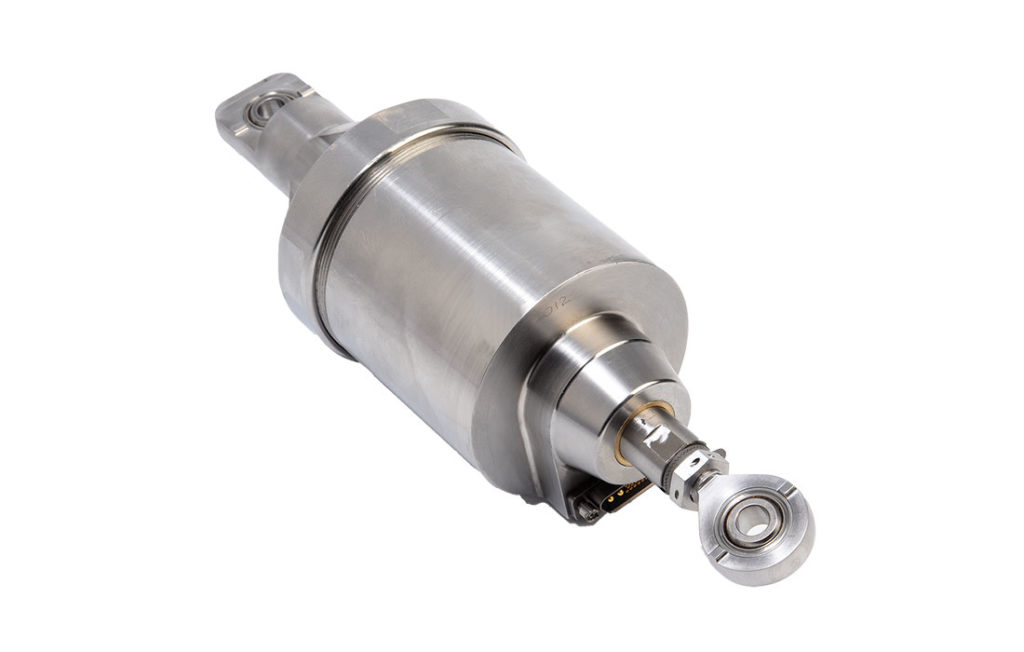
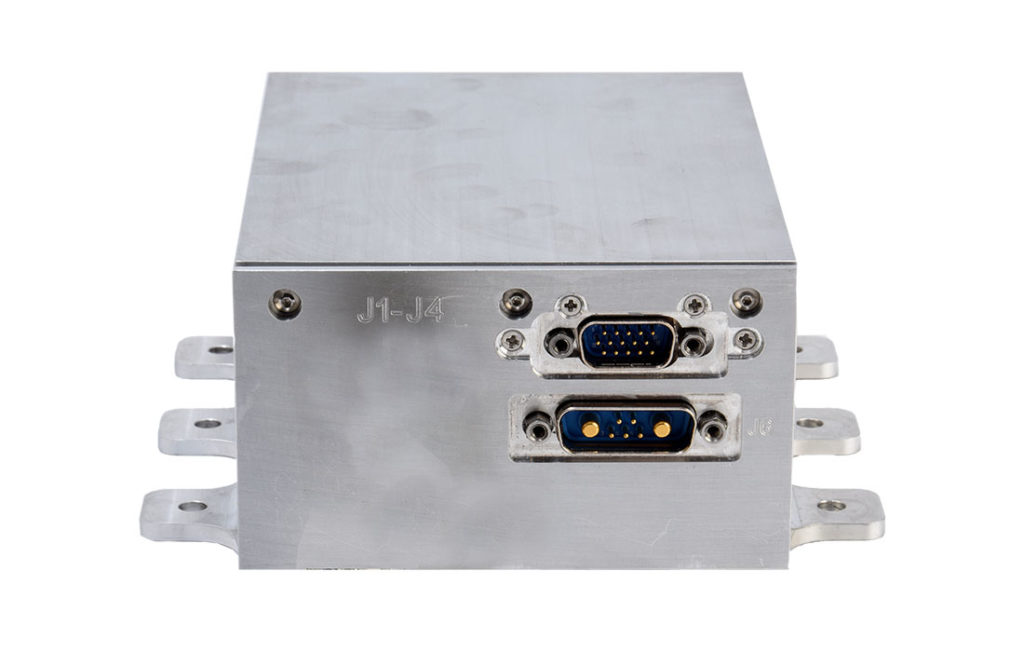
Electronic Features
- 30 amps per channel
- 4 axis 240V min
- Control Type: 4 Quadrant
- Servo Type: Voltage Control
- Relative position loop
- Aux port for downloads & test capability
Mechanical Features
- Mechanical efficiency: 85%
- < 2.5″ motor diameter
- Concentric EMA design
- No gearing
System Performance
- No Load slew rate >200 deg/sec
- Loaded slew output power >2.1 HP
- Stall Torque: 6,720 in-lbs
- Frequency response: >23 Hz
- Angular travel: +30°, -10°
Miniaturized High G Projectile Actuation Systems
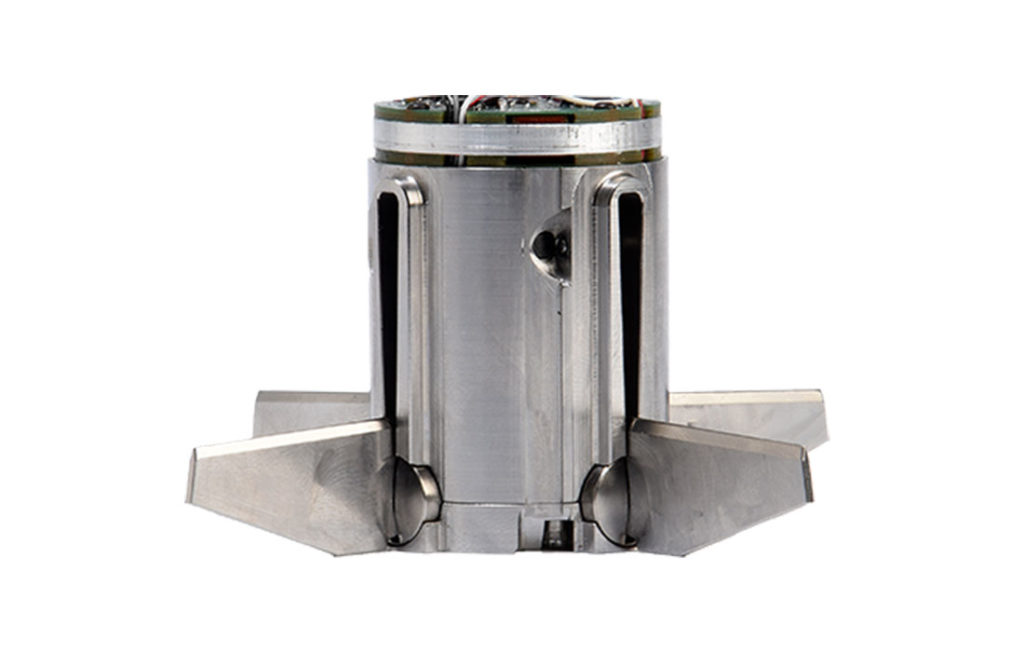
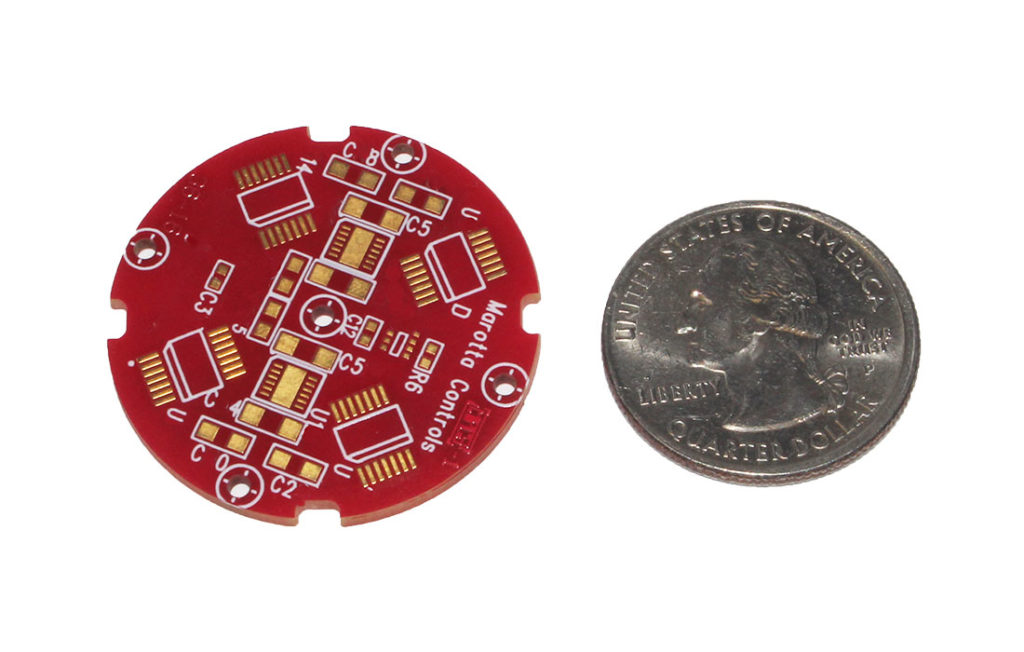
Electronic Features
- 4-Axis 13 to 18V, 1 Amp per channel
- Servo Type
- Position Loop
- Voltage Control
- Bus Compensation
- Relative position loop
Mechanical Features
- Slider/Crank transmission
- Fin stow, deploy and lock capability
- Integrated design solution
- 1.3″ D x 2.0″ L
System Performance
- High G: > 25,000 G
- No load slew rate: >1800 deg/sec
- Loaded slew output power: >0.5 mHP
- Stall Torque: >0.5 in-lbf
- Frequency response: 60 Hz, +/- 1º, -3dB
- Angular travel: +/- 20º
Patented Shape Memory Alloy Fin Lock
The SMA pin puller is a patented technology and has the ability to be unlocked using a non destructive low current pulse which allows a system to be tested in the all up configuration. Once final testing is complete the SMA pin puller can be manually reset to the locked position.
- Non-pyrotechnic
- Manually resettable
- Test mode capabilities
Fill out the form below to download SMA-Fin-Lock
On-Site Analysis & Testing Capabilities
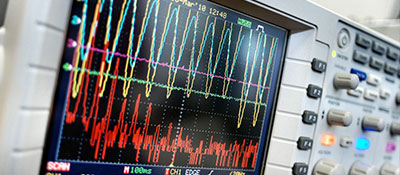
Analysis
- Servo performance
- Available for 6 DOF support
- Kinematics analysis
- Gear train analysis
- Motor performance analysis
- Power/Duty Cycle Analysis
- Circuit analysis
- Simulation, tolerance, derating
- Mechanical analysis
- Stress, thermal, modal/vibration/shock
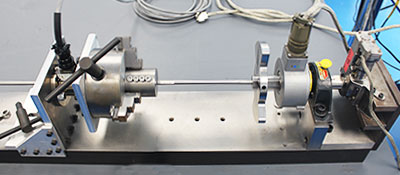
Servo Model Simulations
- Bandwidth/Frequency Response
- Stiffness/Dynamic Stiffness
- Position Accuracy
- Stall
- Step Response
- Stability
- Threshold
- Hysteresis
- Monte Carlo
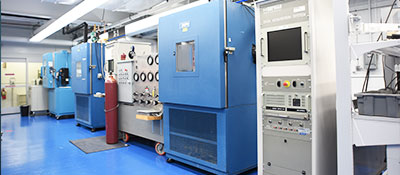
Testing Capabilities
- Proof of Concept
- Component integration and test
- System Integration and test
- ATP and ESS testing
- HALT/HASS
- Software qualification
- Development testing
- Altitude testing
- Vibration testing